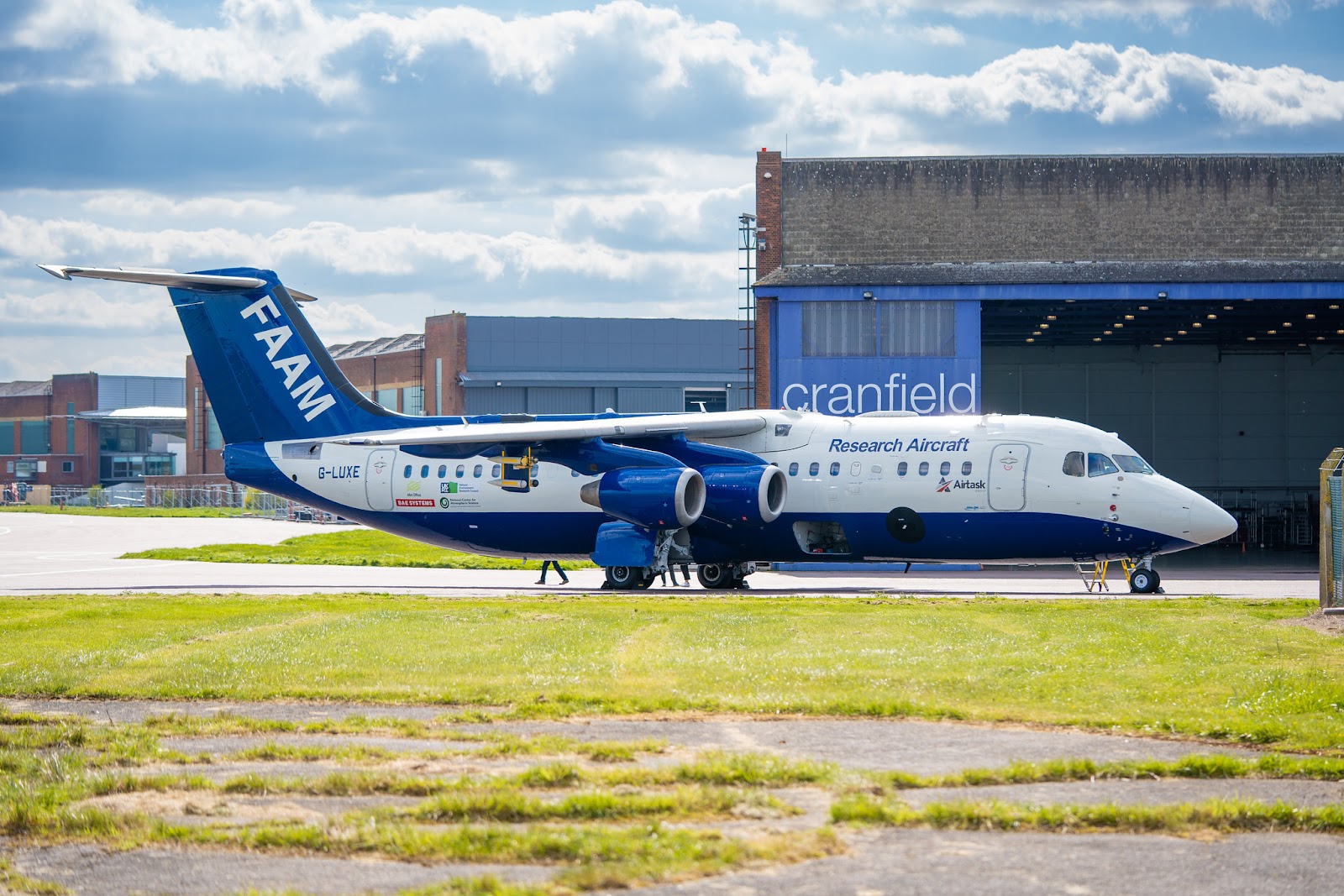
Engineers and scientists have been looking at how the air conditioning systems function on board the FAAM Airborne Laboratory’s research aircraft.
Large aircraft cabins need an appropriate Environmental Control System (ECS) to manage specific temperature, pressure and humidity loads, in order to keep the environment on board comfortable for the crew.
If an aircraft is modified or carries large equipment – like our research aircraft – the ECS may no longer be the right size to meet the demands.
Why does our aircraft cabin get hotter than usual?
Balancing modifications for better science delivery with the needs of our crews, specifically in keeping them cool during campaigns, is an ongoing challenge when operating our research aircraft.
Most of the high-powered scientific instruments, sensors, and supporting equipment inside the cabin get very hot. They also need to be grouped in the front of the aircraft to get the highest-quality data, as this reduces ducting losses, particle contamination, and the aircraft’s body-wake interfering with data probes.
Clustering these heat-producing instruments toward the front of the aircraft means the cabin has a different heat profile to what the ECS was originally designed for.
Instruments inside the cabin also need a scientist nearby to operate them and monitor the data outputs. If the cabin is hotter in this area, it can create a very uncomfortable working environment.
Handling the changed heat profile by modifying our Environmental Control System
The ECS itself has also needed changing to support scientific data gathering. Conditioned air pipes near the data probes have been rerouted, and space- and weight-saving meant the overhead luggage bins needed to be removed, and the accompanying air conditioning ducts which improve distribution that would normally supply air directly to seats were removed with these.
Complicating matters is that during a single flight, the FAAM aircraft often repeatedly ascends as high as a typical airliner (35,000ft) and descends down to near surface (50ft) multiple times. It does this in some of the hottest climates, and at an airspeed (referred to as “science speed”) that is slower than its design cruise. This means the aircraft cruises with its nose up, which concentrates heat on the underside of the aircraft and can heat the floor from below.
Future-proofing the Environmental Control System
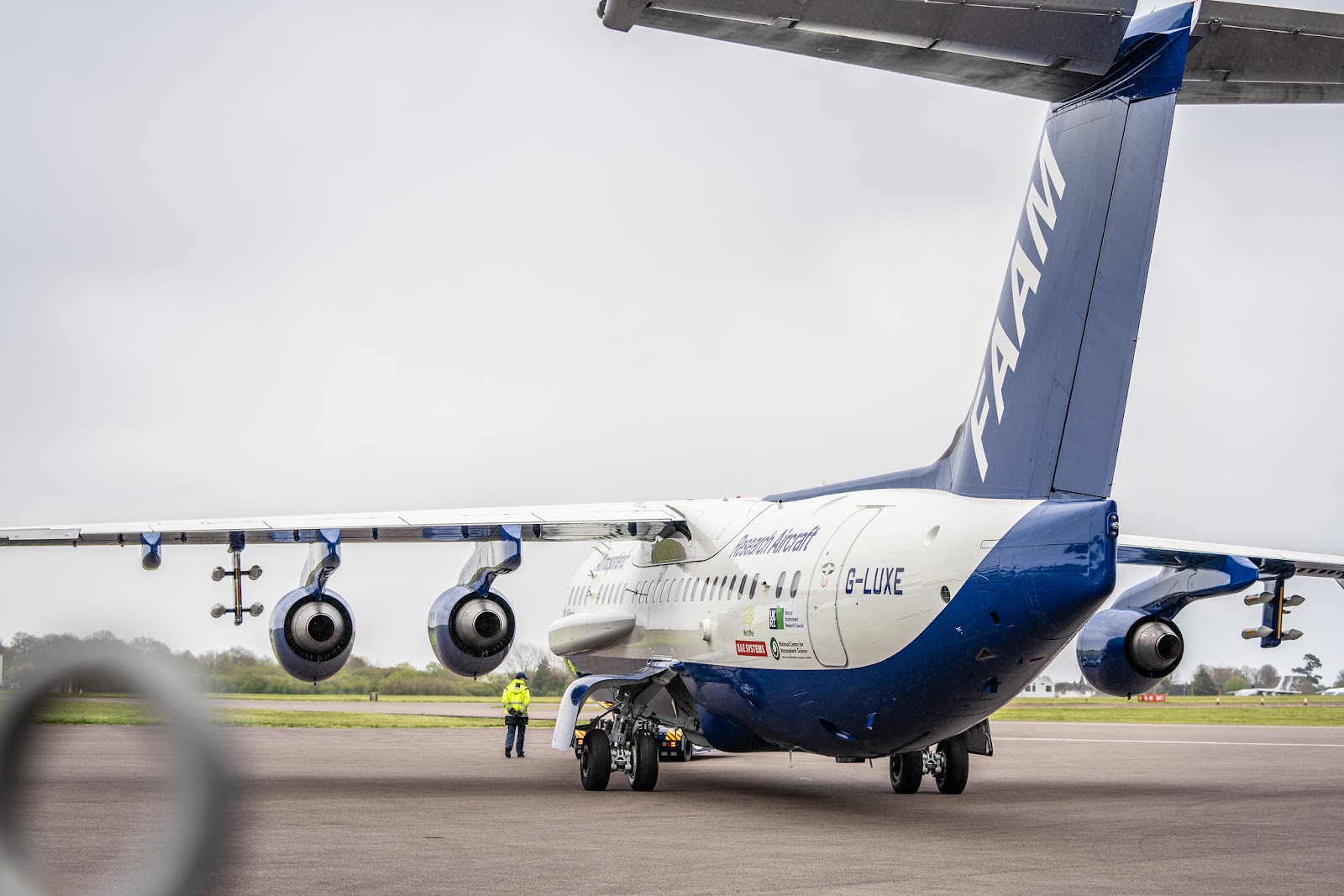
Because the Mid-Life Upgrade will enable the FAAM aircraft to carry newly-developed science instrumentation, we need to ensure the ECS is future-proofed to cope with the wider and less consistent cabin heat profile. We are partway through these efforts, having taken time during the M-Phase campaign in 2022 to develop a more accurate map of heat sources in the cabin. More recently we’ve determined just how much cooling capacity we have available and where. We subsequently conducted a ground-test to survey the ECS output (air volume flow rate) from each duct along the cabin length. While the majority of the power is concentrated towards the rear, the ECS overall has sufficient cooling capacity to manage the expected equipment and climate for the future; it’s a case of redistributing it appropriately.
In the short term we have been able to strategically limit some vents where cooling capacity is not needed, and this keeps the temperature more even across the cabin. However in the long term, to deal with higher-powered equipment and hotter climates, we are now starting to look at ways to introduce new options for air distribution that factor in the aircraft’s modifications. Further work with BAE Systems identified minor rectifications to the ECS that have provided improvements in the air flow performance throughout the cabin. We’ll continue to capture data during flights to monitor the ECS’ performance.